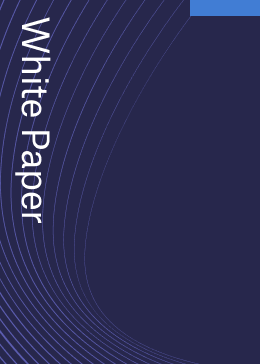
Future-ready and customer-focussed thanks to Made in Germany
By WMF GroupQuality, expertise and performance from a single source – WMF Professional Coffee Machines brings together all its strengths at the Geislingen site
Across the world, the “Made in Germany” quality seal is associated with the values of precision, functionality and technical innovation. For WMF too, these values are inextricably linked to its brand essence – after all, for over 150 years, the company has embodied the “Made in Germany” approach in a way that very few others have. The consistent high quality and well-devised, elegant design of all its products can be attributed directly to the particular set-up used by this global player. When it comes to its professional coffee machines, all the different aspects of production come together in Geislingen an der Steige. From the initial design of machines, add-on equipment and software solutions, to the construction, production and manufacturing stages, right up to service – each process flows seamlessly into the next. And the crucial factor at every stage is that the customer’s interests always come first.
For WMF Professional Coffee Machines, “Made in Germany” is synonymous with a highly concentrated value creation process. Every production step, from the initial idea to the finished product, is coordinated from the company’s headquarters in southern Germany – and the majority of tasks are completed on site. Thanks to this approach, values such as high precision and customer-oriented innovation can be naturally adapted to increasing globalisation and digitalisation. The concrete advantages of a centralised development and production process in Germany can be summarised with the following key points: “quality”, “transparency”, “communication” and “agility”.
Short communication paths and direct feedback in one place
The aspect that benefits most considerably from this approach of pooling all resources at one location is the company’s internal cooperation. The physical proximity between the individual departments and teams guarantees an agile and efficient decision-making process, while ensuring that tasks and responsibilities are coordinated efficiently. For example, during the development of a new product, other departments besides sales and product management are involved from a very early stage – including the service, production and procurement departments. Frank Göltenboth, Vice President Research and Development GBU Professional Coffee Machines, describes this process as follows: “Even during the early stages of defining requirements and developing a concept, all of our departments are actively invited to share their input. This is primarily about implementing what we’ve learned from the past and harmonising any potentially conflicting priorities. The fact that every department involved is based at the same location is an enormous advantage and ensures a high level of process efficiency.”
High quality thanks to concentrated on-site advantages
The fact that the company’s value creation processes are concentrated at one location also forms the basis for the exceptionally high quality that WMF delivers. Wolfgang Putz, Vice President Quality Management GBU Professional Coffee Machines, explains: “Our quality standards are guaranteed thanks to thorough training, a high level of technical expertise and our far-reaching vision, as well as a carefully nurtured sense of personal responsibility and commitment. In order to make the best use of these attributes, a high level of data and process transparency is essential. To this end, WMF consistently relies on closed-loop quality management processes.” Since the development, production, service and quality management stages are all concentrated at the Geislingen site, these processes work particularly efficiently. It means that the combined knowledge and expertise of all employees can circulate quickly and easily within the value chain and can be put to the best possible use at any time. Another factor that contributes to an effective and transparent quality management system is the strict German industry standards and WMF guidelines, which are clearly reflected both in internal processes and in the selection of suppliers.
Another indispensable guarantor of quality is WMF’s network of its own service organisations and partners, which is the only one of its kind in the industry. It provides important first-hand information from millions of customers, which can then be efficiently pooled, evaluated and implemented in Geislingen – for example, to improve machine design or develop new functions, as well as in the field of customer advice and service.
Sharing ideas early and responding quickly
If we take a look at the process of developing a WMF coffee machine, the advantages of the “Made in Germany” approach become especially clear. Here, the company is not only focussed on achieving maximum quality and precision – in keeping with its brand message “Designed to Perform” – but also on the specific requirements of the customer. WMF Professional Coffee Machines succeeds in the difficult task of balancing consistently high-quality, standardised products with customised solutions thanks to the unique sense of solidarity between its different departments. Thanks to this approach, any input from the customer quickly reaches the development department, which then promptly communicates with the production department. Alexander Schlee, Vice President Production Coffee Machines, summarises the process as follows: “Due to the close, interdisciplinary consultation between colleagues, we are able to implement even complex requirements at short notice – and that gives us a key competitive edge. We also discuss how we can optimise existing solutions on an almost daily basis. This constant flow of ideas is put into practice in production very promptly, as our production and assembly sites are literally on our doorstep and we work with lots of local partners.” This enables the company to achieve quick response times and dynamic change management without any problems. Some assemblies are fitted internally in the immediate vicinity of the final assembly site, though some are also manufactured externally, depending on the technology. In these cases, the high standard of quality is ensured through quality controls at the supplier site and then in Geislingen. In addition, the vast majority of turned and sheet-metal parts are manufactured directly on site. “For one thing, we rely on specialist in-house expertise, such as in the production of our grinder discs. And with around 3000 different sheet-metal parts for various functional and design elements, we also have a high level of flexibility, which enables us to respond quickly to customer requirements,” explains Mr Schlee.
Software made in Geislingen
Of course, this concept is not just limited to the machines themselves. The WMF software department, which is also based in Geislingen an der Steige, assists in the development of innovative hardware and enables the company to position itself as a full-service solution provider. This form of in-house development is an essential unique selling point within the industry. The “Made in Germany” approach is also central here: due to its physical proximity, the software department is perfectly integrated into every process. The close coordination within the control loop, which consists of sales, product management, software development, quality assurance and service, enables a high level of agility and flexibility. “From our Geislingen site, we develop software solutions for the entire world. Together with our on-site colleagues and partners, we adapt to local needs and trends, such as WeChat Pay and AliPay for China or GoPay for Indonesia, and implement suitable digital solutions in cross-border teams. The project coordination for this is concentrated in Germany,” says Benjamin Thurner, Vice President Business Development Digital, GBU Professional Coffee Machines.
The company also works closely with universities and research institutions to ensure that it is incorporating the latest IT knowledge. Software solutions are often not standard products and need to be adapted to specific customer requirements – factors which make these efficient processes and external contributions are all the more relevant. What’s more, the field of digital solutions increasingly holds potential for innovations that improve the functionality of machines. Telemetry platforms such as WMF CoffeeConnect, which offer operators exciting opportunities to optimise their processes and boost their profits, are therefore fully in line with the values of “Made in Germany” – not in spite of, but rather because of their global connectivity. “The economic advantages of digital solutions are increasingly becoming a priority for many WMF customers. And the pandemic has accelerated this trend once again – for example, with contactless ordering and payment processes. With our solutions, we’re connecting coffee machines around the globe, thereby improving our customers’ daily business as well as their prospects for the future,” continues Thurner.
Patented innovation
The importance of these new forms of technology for WMF Professional Coffee Machines is also reflected in the impressive number of patents that the Geislingen-based engineers have already been able to register. A review of the last few years clearly shows that this is not a case of innovation for innovation’s sake. For example, WMF espresso took “barista-made coffee” to a whole new level of process reliability. Meanwhile, the “Fresh Filtered Coffee” technology option, which was introduced in 2019, enables operators to offer delicious filter coffee and espresso-based specialities from a fully automatic coffee machine. The “AutoClean” system, which was recently showcased at the Internorga trade fair, revolutionises and dramatically simplifies the machine cleaning process. WMF’s new hardware components and software solutions are therefore always developed with the aim of creating real added value for both operators and end customers – an aim that perfectly complements the values of “Made in Germany”.
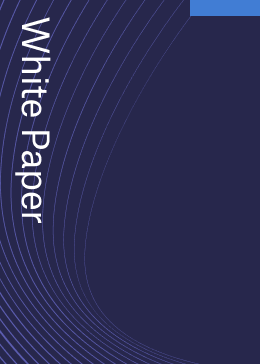